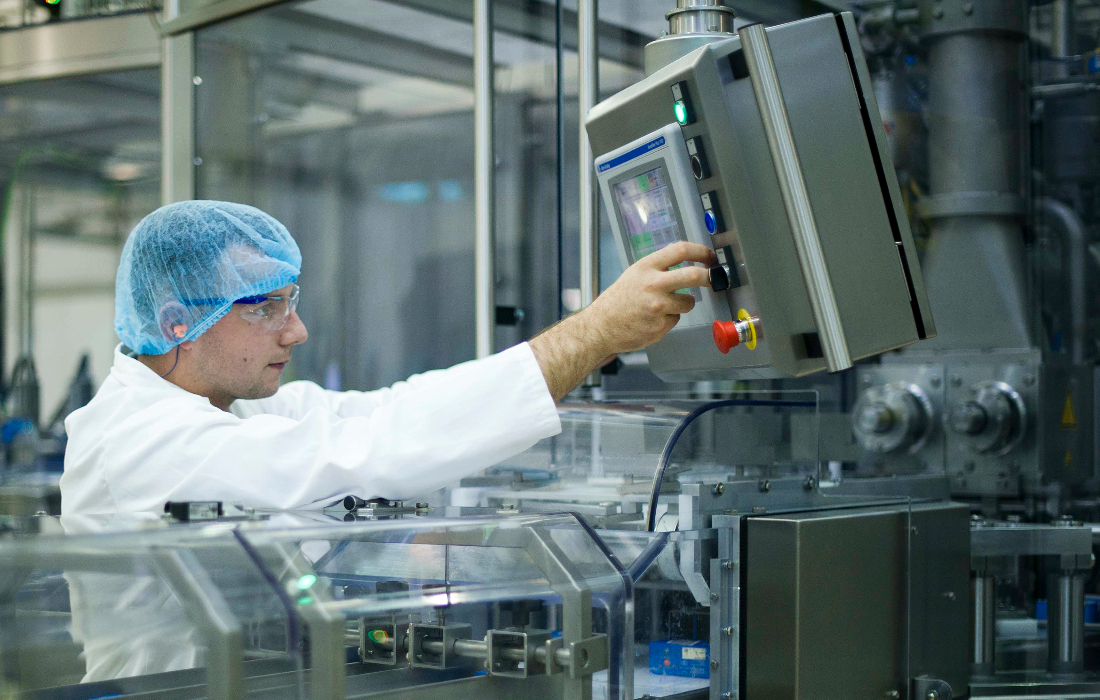
The manufacturing industry is awash with challenges, but with food and beverage being the largest manufacturing sector in the UK – bigger than automotive and aerospace combined – it’s no surprise that this arena faces proportionately increased challenges.
The ‘Food & Beverage: An Industry Review’ in-depth report from RS explores some of the key factors affecting the industry, from the economy and sustainability through to skills shortages and innovation, to help this mammoth sector navigate them. Using insights from a variety of sources as well as RS’ own research, the report combines the state of play, outlines the impact of the current economy and highlights the opportunities for F&B players.
F&B is vital for the UK economy
The role of the food and beverage sector in the UK economy mustn’t be underestimated. The output was valued at £33bn in 2022 and the sector is made up of more than 12,000 businesses comprising 97% of SMEs.
Millions of jobs rely on the industry, so the requirement for a real focus on how the challenges can be tackled and a collaborative approach is crucial. The only certainty for this industry right now is uncertainty.
With no crystal ball and many organisations concentrating more on overcoming the challenges of today than planning for the future, opportunities for innovation could be lost and much-needed investment for innovation that can drive efficiencies could be side-lined in favour of running the tightest ship.
There has been evidence of this, according to RS, which states that over the last 12 months, it has seen businesses close sites to consolidate or streamline operations. Sadly, the ones that have closed altogether are the SMEs. But RS’ report showed confidence has been on the up throughout 2023: in the first quarter of the year, only 14% of businesses in the sector believed conditions had improved, which increased to 26% in the second quarter. By Q3, more than 90% of large businesses expected conditions to remain the same and more than 40% of smaller firms expected improvements in business conditions.
Finding solutions to labour shortages can help the quest to ease cost pressures
Finding ways to ease cost pressures is key, especially at a time when cost increases for F&B manufacturers are higher than the price increases. Better management of energy consumption and implementing proactive maintenance strategies for increased plant efficiency and downtime reduction are key areas to focus on. However, the impact of labour shortages is a real factor for this sector and outsourcing maintenance to help overcome these challenges is a proven way to tackle cost pressures.
RS worked with a global food products provider for which it undertook an audit of assets of one of the firm’s sites. Focusing on one of the most critical plant assets, it identified excessive noise from the asset which indicated an issue that the firm had not taken any preventative action on.
The fault was identified, remedied during planned downtime to avoid disruption and another defective part was replaced at the same time, prevent reoccurrence. Because the parts used are subject to a long lead time, RS also recommended these critical spares be ordered in and kept on-site in case of a future issue. Had the issue not been identified and failure occurred, the downtime costs would have run into tens of thousands of pounds.
The value of outsourcing is clearly illustrated in this case and helps firms find a solution in times of labour shortages, which were highlighted in RS’ Indirect Procurement Report 2022.
In it, one in three respondents to the survey said finding the right staff was a problem, and attracting and retaining them was one of their biggest challenges. Sector output is drastically affected by this situation and the problem is more prevalent in more remote areas of the country, where F&B manufacturers struggle even more to access talent.
Outsourcing at a time of financial difficulty may be perceived as added cost. However, F&B manufacturers must be willing to make the investment and take the right action to negate risk of bigger issues that can result from a reactive maintenance approach.
Workforce churn is adding extra pressure in areas like health and safety compliance
Workforce churn is having a real impact on health and safety compliance, according to RS’ report, as a high turnover of staff makes compliance with standards more difficult. Staff retention measures like training and development, and workplace culture, are areas to home in on.
An important element in staff retention is an organisation’s approach to PPE. Getting fit-for-purpose PPE that fits the wearer – regardless of size, gender and cultural requirements – and which meets standards are key to the quest to attract and retain employees, said RS.
ESG is a top agenda item
No firm in any sector can afford to side-line ESG, and the majority see it as important to delivering their company strategy: as cited by nearly 80% of respondents to 2022’s RS and CIPS Indirect Procurement survey.
Organisations are increasing commitment to ESG strategies from decreasing energy consumption to reduce carbon output, using more sustainable products and actively seeking to work with suppliers that can demonstrate a sustainable supply chain. It’s also a good way for firms to gain a competitive edge.
The reduction in energy consumption as a carbon output reduction measure is also clearly a business benefit with regard to cost savings. And firms that implement digital technologies to gather consumption data to help them improve performance will reap the benefits of any such investment.
RS worked with an organisation in the F&B sector whose water usage and wastewater disposal were significantly reduced after RS designed a plant monitoring system. Data from relevant assets is continuously uploaded into the RS Industria cloud application. This allows for monitoring and setting of parameters that can alert engineers to issues and allow them to investigate and act quickly.
The outlook for industry players is mixed but, from the findings of the RS report, it is clear that collaboration and building partnerships will be key to helping F&B operators tackle the current and ongoing challenges, and keep business thriving.
The full report ‘Food & Beverage: An Industry Review’ can be downloaded here.
Bagikan Berita Ini
0 Response to "key challenges facing food and beverage manufacturers - The Manufacturer"
Post a Comment